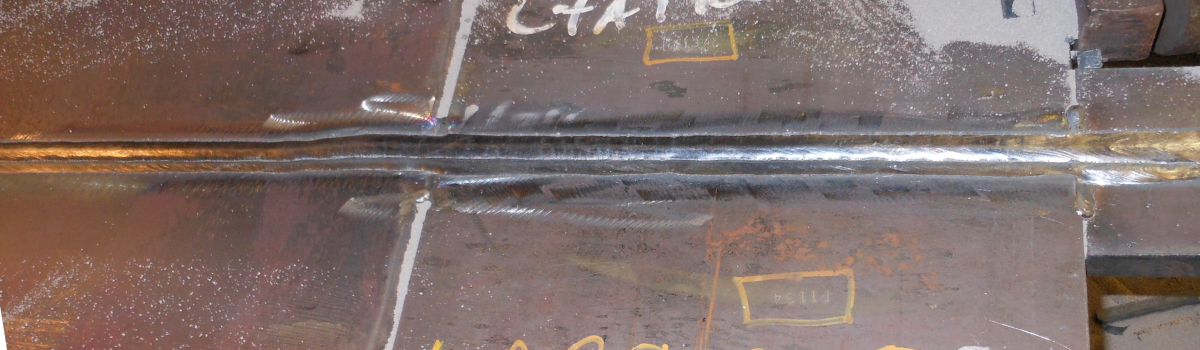
Weld Procedure Development
Our capability to develop weld procedures draws on years of production knowledge & needs to design and qualify project specific procedures that are then subject to testing by NATA certified third parties to ensure compliance with pressure equipment standards and bespoke project specifications.
Weld procedure development benefits from being done by personnel who do it day in day out. Our stand alone ‘weld procedure development service’ brings together practice and theory enabling specialised procedures to be developed that can include job simulation mock-up, pre-heating or cooling as encountered with live gas pipeline welding scenarios.
Drawing on workshop capability, we have the capacity to develop weld procedures for SAW, GMAW, GMAW STT, GTAW and MMAW integrating a wide range of materials and welding consumables from basic carbon steel to high strength alloys. Testing services can be customised to include specific needs such as additional mechanical or corrosion tests frequently present in project specifications.
We are currently developing a digital solution to upgrade our welding management system drawing on emerging digital twin theory and SQL database architecture to support intuitive identification of available procedures taking into account the wide variety of criteria and relevant essential variables from the Australian standards and ASME codes covering pressure equipment and pipelines. This functionality enables our team to quickly assess weld procedure requirements against our extensive procedure library and welder qualification status.
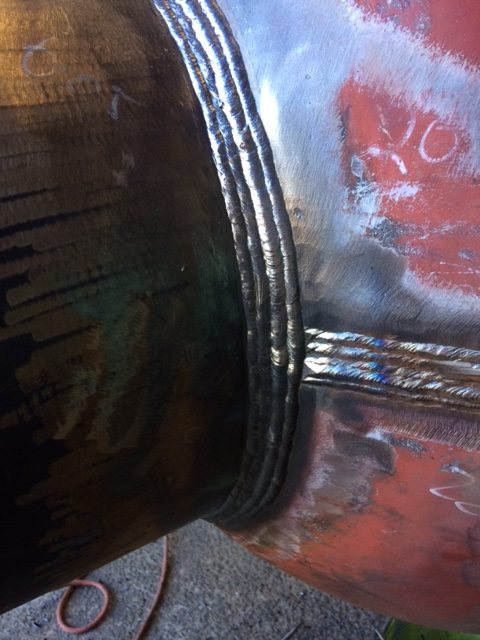
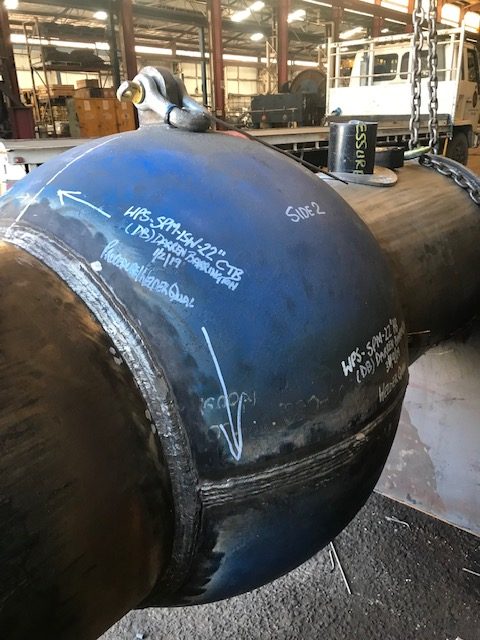
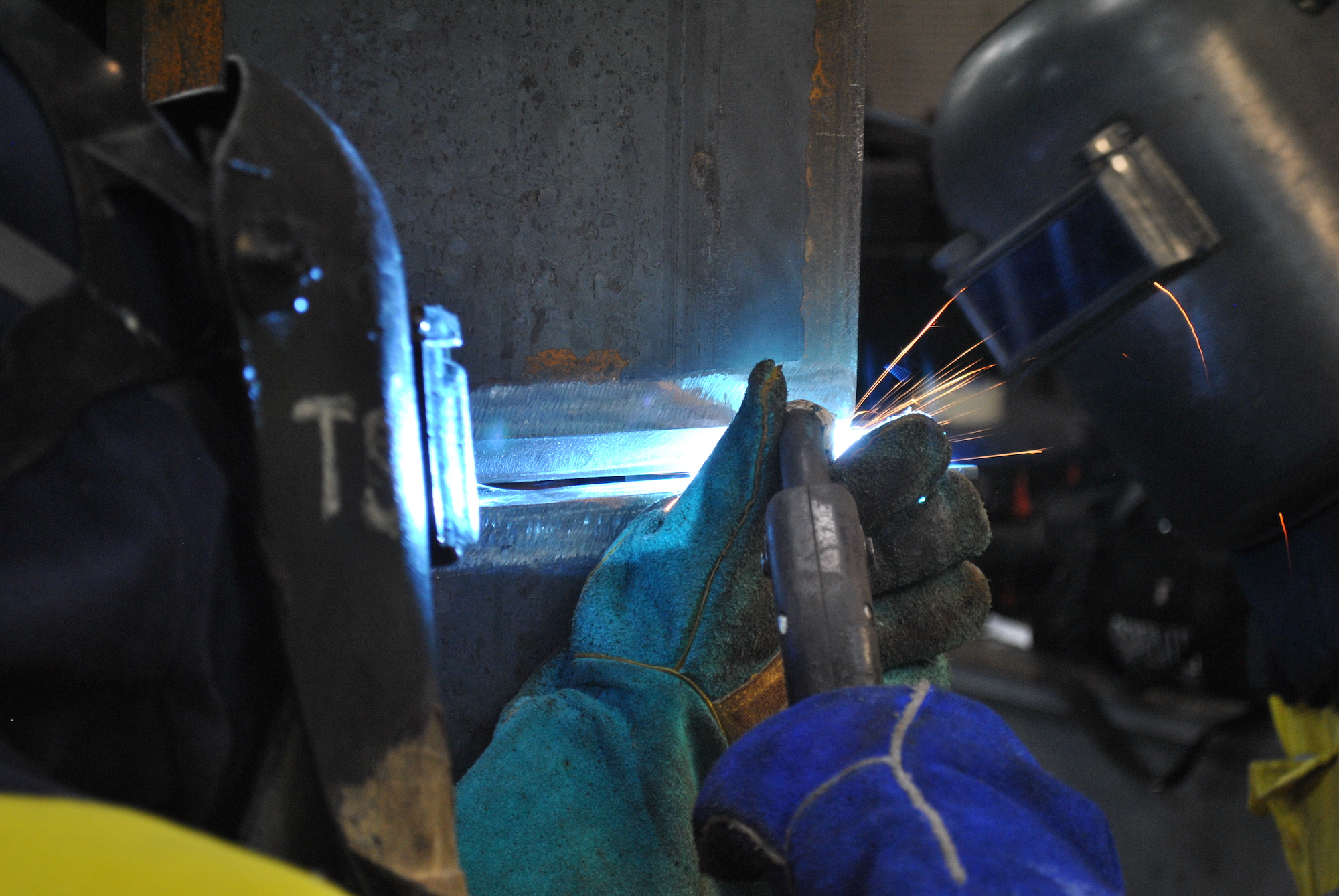
Case Study
Completed 2019
Packinox Bundle Replacement Project
The refurbishment of Caltex’s Packinox heat exchanger required a bundle replacement to solve efficiency problems.
To do this the 80mm thick head needed to be cut off then re-welded into position.
With asset down time being costly an accelerated welding method was required to be able to complete the refurbishment within a planned refinery shutdown window.
Request a Quote
Please allow at least 3-5 business days for us to prepare a budget estimate