Introduction
Digitalisation of the workforce was one of the many shifts that made us reconsider the nature of our industry as the need for a different type of worker became more apparent. The expectations of an employee have also changed, where cross skilling is now a common practice of the workplace regardless of industry and company. Not only is cross skilling a wise financial decision for a business, it also allows for employees to venture out and gain new skills that they would otherwise not have the opportunity to do. These opportunities only rise with exposure to the different industries and people, where these learned lessons are then invested back into the business, which emphasises the beneficial longevity in cross skilling.
Adapting to change
With the workplace becoming more digitalised, it is important for a traditional industry like ours to adapt to the changing needs and capabilities of both our clients and employees. There has been a definitive shift in the workforce where employees are no longer required to specialise in one role, as knowledge, and to a lesser extent, skills, are viewed as a commodity as a result of the internet and connectivity. This results in workers now needing to be able to differentiate themselves from competitors who might complete a task more efficiently and hence for cheaper. Expectations have changed where workers now need to diversify their skill set and achieve a myriad of different tasks despite being hired for a specific role. Typical expectations of a role may change drastically within the next few years and we could see a major overhaul compared to where we are at today. Whether good or bad, it marks the start of a changing workforce and the need for workers to adapt accordingly.
The Benefits of Cross-Skilling
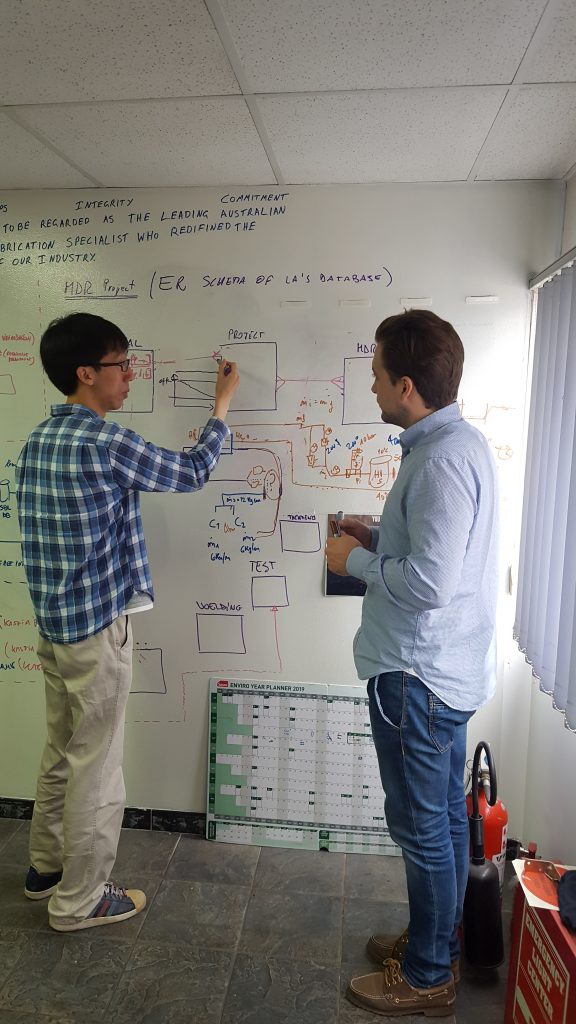
Cross skilling is becoming essential to the workforce as it teaches employees skills which they can apply to future projects. And with the inevitable start of I4.0, it reaffirms the need for us to update our current workplace structures to provide opportunities for our workers to cross skills. This is recognised within our own R&D team. As a data scientist accustomed to dealing with the expected responsibilities of data, Ming Zhao was able to find stimulation in a new role that required him to learn about the practical aspects of manufacturing and data acquisition rather than just the pure technical aspects of data science. It changed his perspective on the role and broadened his subset of skills as he gradually learned what it meant to be hands-on – an experience he did not have with previous roles. Similarly, as a mechanical engineer, Antonio Zanin would not have expected his role to intertwine with those of a data scientist. Yet, the collaboration between these two R&D focused employees emphasises the multifaceted growth that individuals can have as they branch out into different professional areas.
Cross skilling is not just beneficial to a business. It can also be the perfect work structure for those who are looking to expand their work repertoire and skills.
The collaboration between Ming and Antonio was inevitable from a business perspective as our processes started to become more digitised as we moved further into I4.0. By providing an opportunity for the two different industry-based employees to collaborate, we gained two redefined employees by learning different industry skill requirements. This opportunity emphasises our position as industry leaders as we pave the way in redefining traditional roles in a manufacturing field to encapsulate both conventional and modern techniques.
The Importance of Cross-Skilling
As a conservative industry, it is vital for us to understand who is willing to cross skill and take the next step in advancing themselves as a worker and for the company. As an ‘older’ industry, it is expected we have workers who may lack current digital knowledge possessed by the younger generation. Hence, cross skilling provides an opportunity for these workers to learn vital skills that last for life, especially with digital skills that can be used both in a professional and personal sphere. It is also important for both the older and younger generation to be open to this chance of improvement as it helps to bridge the gap between individuals and generations. To those who are planning to stay in the same role in the next five years, 40% of the core skills are expected to change (World Economic Forum, 2020), which supplements the need for workers to move forward according to expectations. These advancements are not purely limited to the manufacturing industry as it is applicable to every role, employee, business, and industry.
Teaching Cross-Skilling to Individuals
Every employee is a different individual and we must understand the workings of these people to know who can be cross skilled and who cannot. This shift also allows employers to differentiate between those who are looking to upskill and diversify their current capabilities versus those who lean towards complacency. “Employee performance can be manifested in improvement in production, easiness in using the new technology, highly motivated workers” (Vasanthi, 2008). However, how do we get these types of workers in the first place? Not only do we need to provide employees access to these technologies, but we also require those who are looking to further themselves as an important part of the business.
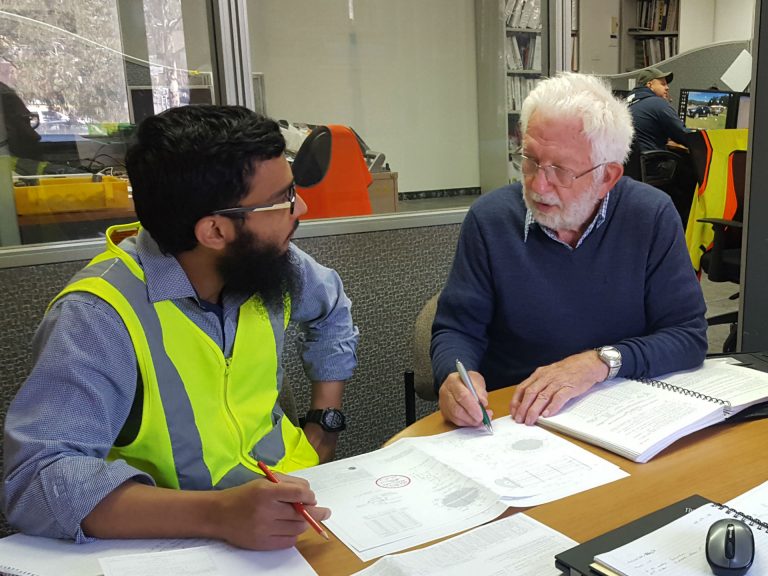
Cross skilling is not only beneficial to the individual worker but also vastly improves team coordination and dynamic. Cross skilling targets ‘single points of failure’ (Vasanthi, 2017) and reduces the chance of failure in complex tasks as it ensures that every person on the team is capable of completing a job and is not solely reliant on the specialised individual. This prepares the company for all types of scenarios, as well as saving time and resources as there is no need to bring in external workers.
How it benefits our business
As a business, we should redefine the role of an employee and promote an innate sense of learning by emphasising the benefits of cross skilling as a way to further an individual’s own capabilities. Facilitating the newfound passion to learn will also act as a dual means to share organisational values and stimulate a company culture of collective unity towards objectives (Gawali, 2009). This inherent desire to learn will only benefit the company as it stimulates a genuine passion to better both the individual and company, which will only translate into the offered products and services.
Conclusion
Therefore, we can see that cross skilling is an important part for any business and its employees to develop and further itself in a changing workforce. Though it may be difficult due to the need to cater to certain individuals, this should not detract from the immense benefits it will have on both the individual and the employer as it emphasises the need for growth on both ends. It is important for us to show the potential in employees as similarly we reap the benefits in these learned lessons.